How Do You Choose the Best Solution for Your Cleanroom Floor?
By Matthew Korkuch and Chris Hohn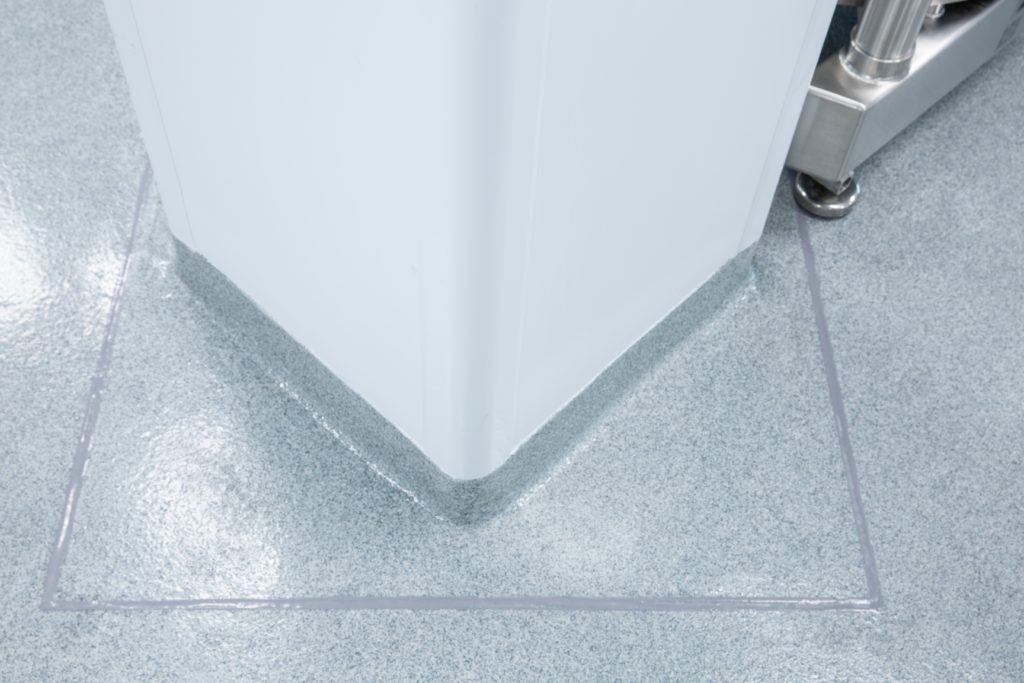
When designing a new modular cleanroom space, facility managers are often unsure where they stand on proper cleanroom flooring. Epoxy? Or sheeted flooring, like rubber or vinyl?
At first glance, the advantages and disadvantages of each in cost, maintenance and effectiveness can be overwhelming. While we do not design flooring at AES Clean Technology, we have worked with all cleanroom flooring types and our cleanroom technology experts can help you take the risk out of finding the best flooring solution for your next cleanroom design build.
The good news is that there are plenty of great options in both cleanroom epoxy flooring and cleanroom sheet vinyl flooring—and they are all compatible with AES cleanroom systems. Of course, your ultimate decision will come down to your specific use case and current good manufacturing practices.
Cleanroom Epoxy Flooring
Many consider epoxy flooring the top-of-the line solution—and for good reason. Epoxy floors certainly look great, and they are known for durability and relative ease of maintenance after building a cleanroom.
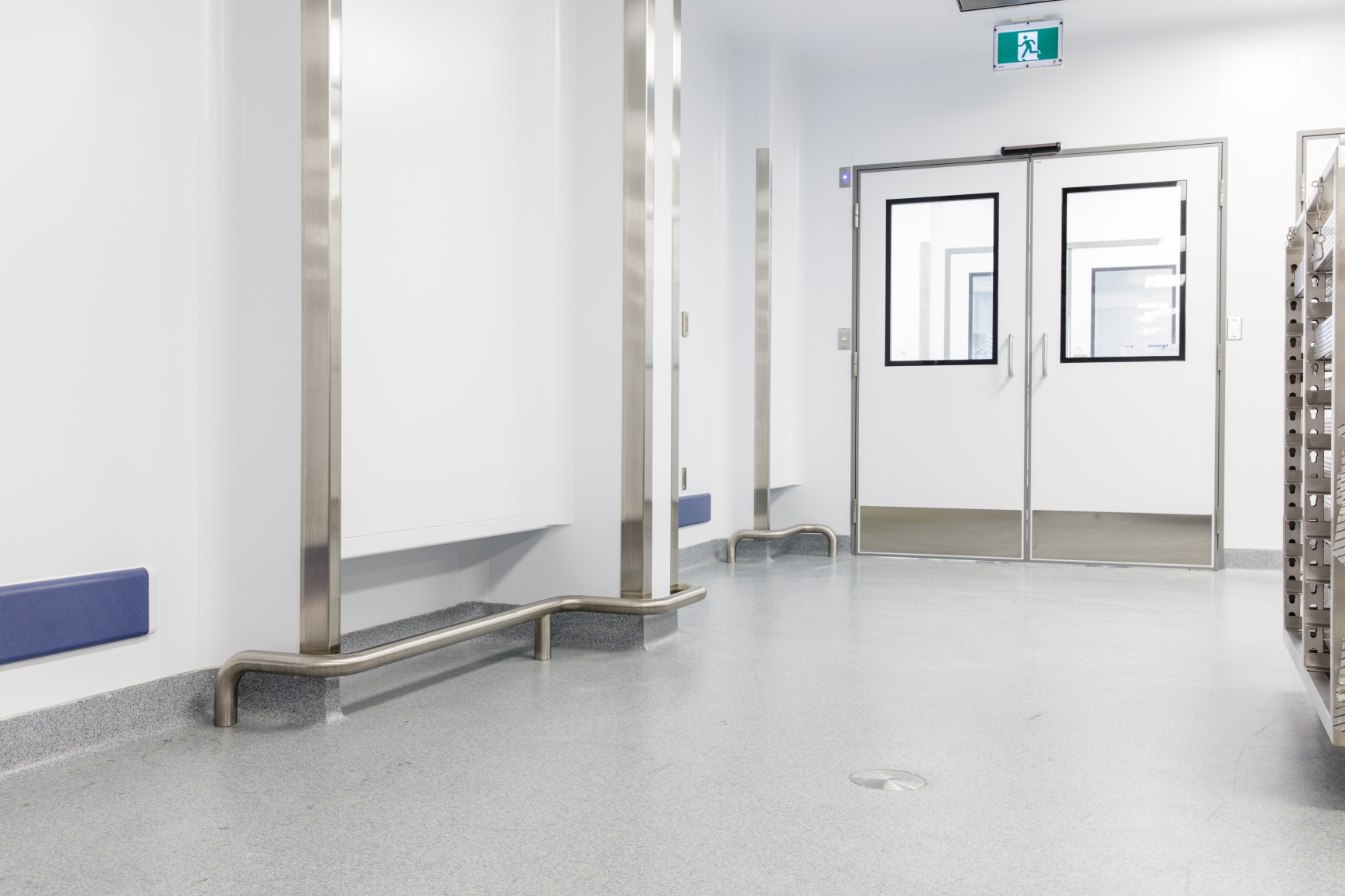
Typically, epoxy floor is laid in a series of five pours, beginning with a base layer, which is engineered to smooth out any imperfections in the slab, and ending with a topcoat, which can be modified to improve traction. As the individual liquid layers cure and harden, they provide a solid, uniform barrier. There is an art to pouring epoxy flooring, however, so the interface between floor and wall requires an expert’s hand to get a perfect result.
Epoxy floors are generally low maintenance. They will withstand rolling carts with relative ease, and its layered nature means that even worn areas will retain its look and color over time. If there’s an accident—from a hammer drop or a gouge from heavy equipment—installers can easily spot-repair damaged sections.
Expense is often the biggest concern—and even there, it really depends on your use case. Simply put, more cleanroom walls require more labor, which is what will drive installation costs. In large open spaces, however, epoxy flooring is actually price-competitive with cleanroom vinyl sheet flooring.
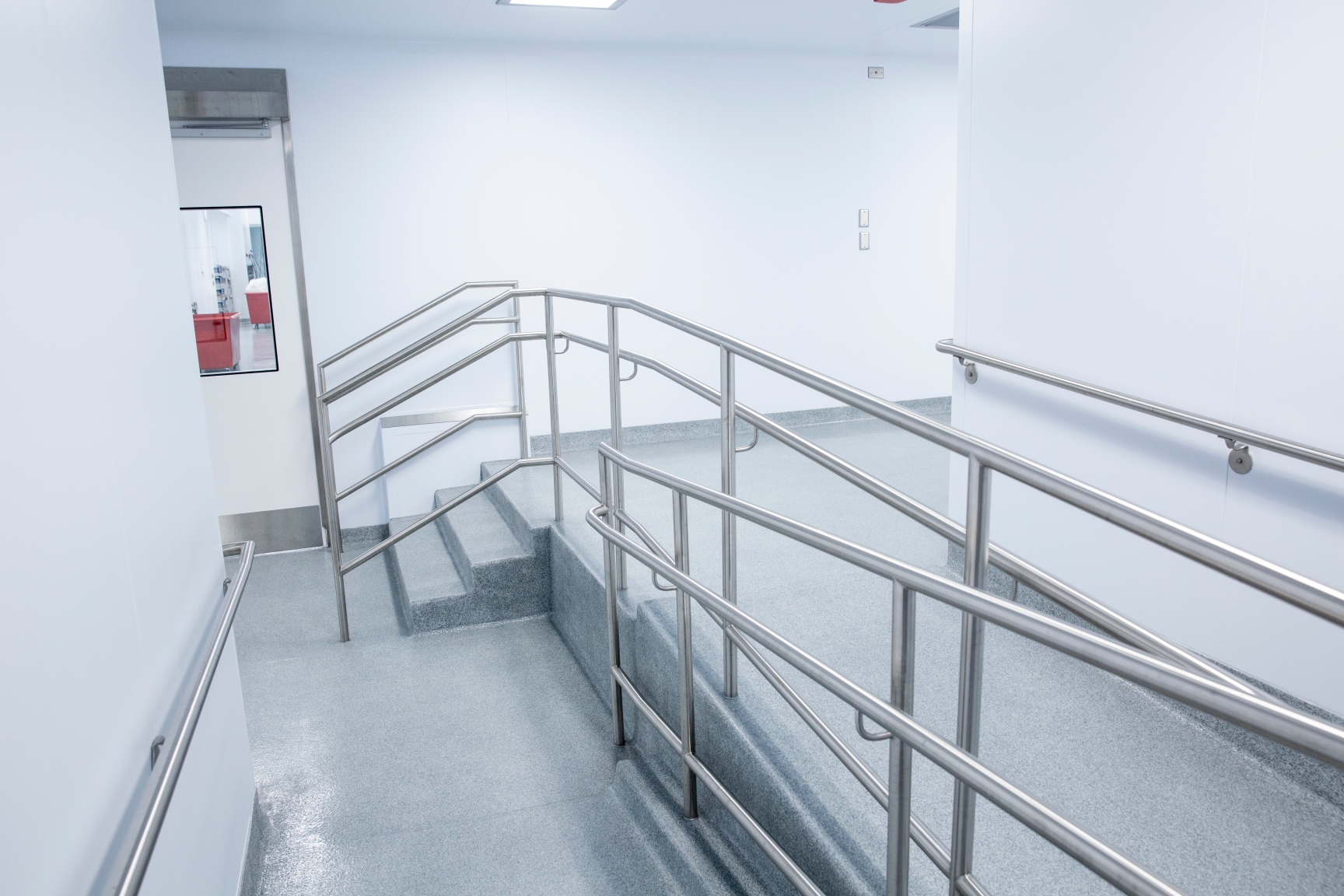
Cleanroom Vinyl Sheet Flooring
Installing vinyl requires far less specialized labor, but it does require preparing the cleanroom floor with a consistent substrate to provide the best results and added cushioning. Like your home flooring, vinyl is laid down in long sheets, which can then be welded—either hot or cold, depending on the manufacturer’s recommendation—to remove the appearance of visible seams. Installers typically add a polyurethane topcoat to provide further protection and remove crevices for dirt to hide.
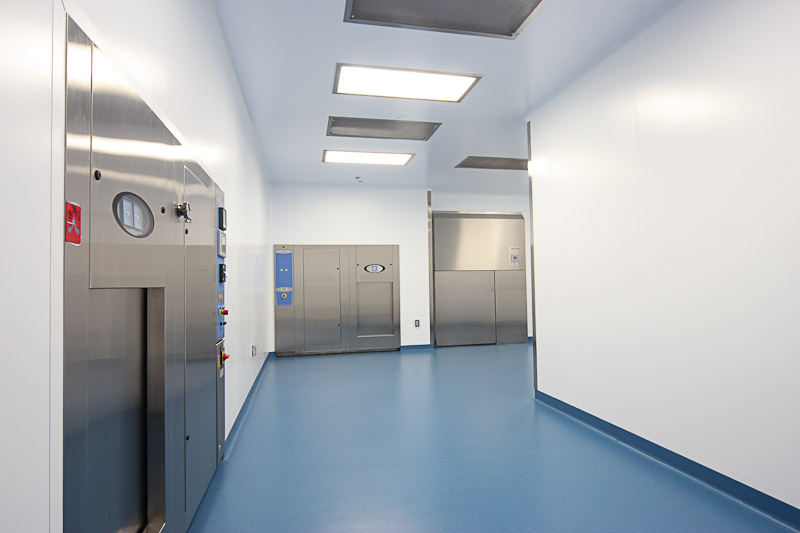
While less resilient to wear and tear, it is a relatively simple process to repair damaged vinyl flooring—simply pull up the damaged vinyl then cut and weld a replacement piece to fit. There is more cushion to a vinyl floor, so cleanroom workers might find vinyl flooring easier to stand on for any long periods of time.
Any Floor is the Right Floor with AES Clean Technology
In recent years, we have found that many of our modular cleanroom customers prefer epoxy floors, overall. However, the choice should really come down to your anticipated use case, including foot traffic, cleaning practices and cleanroom maintenance.
Regardless of whether you choose epoxy or vinyl flooring, either material works well with AES modular walls.
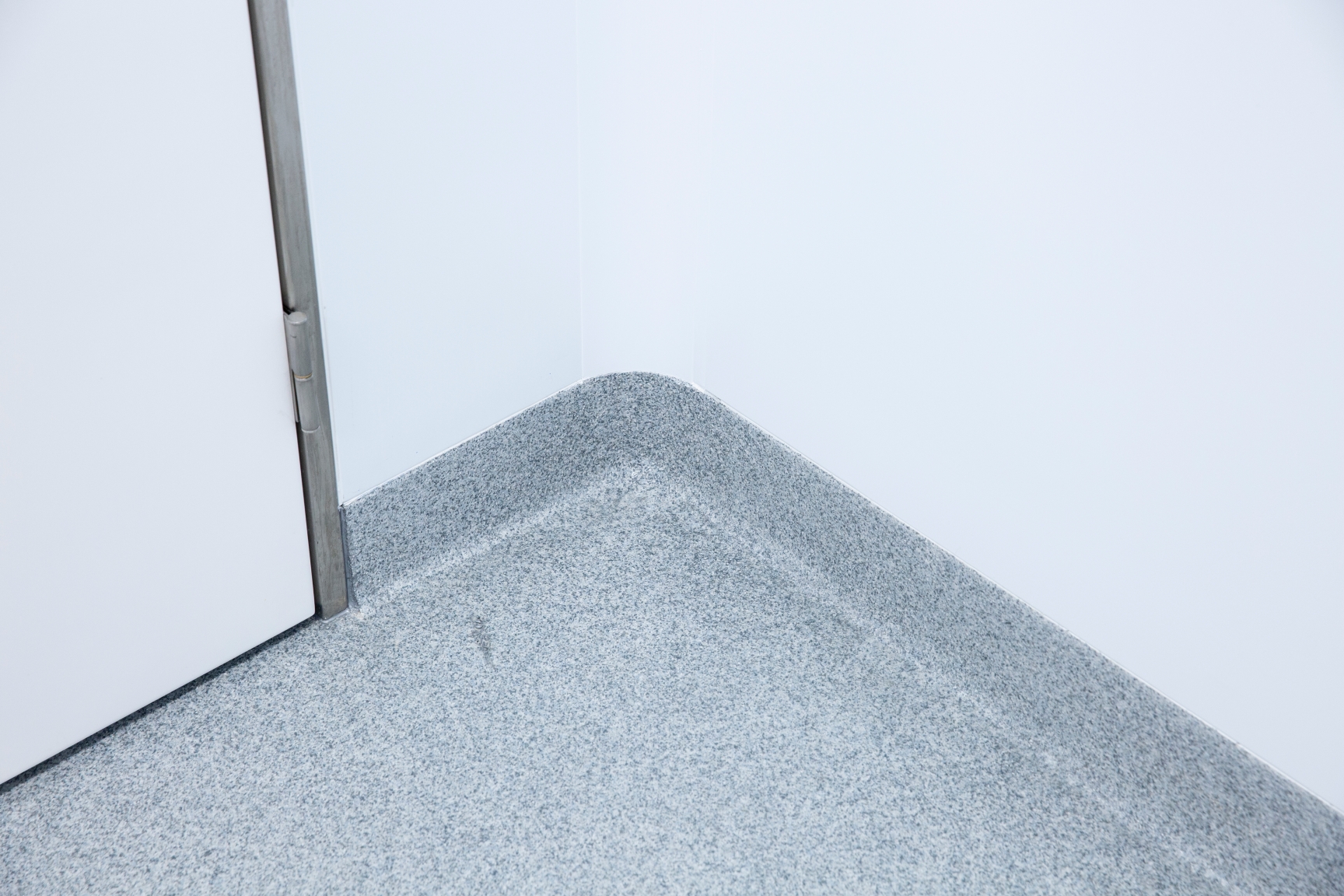
There are plenty of variables to consider when building a cleanroom, from design to construction, but your decision on flooring does not need to add extra stress to a complex situation.
Our best advice is for you to give us a call if you are having trouble making a choice. We have the experience to advise you and your installers in creating a product that will satisfy you and your cleanroom workers for years to come.
Sidebar: 5 Cleanroom Floor Points to Consider
- 1. Constructability – The five-step process of pouring epoxy floors can take up to a week more to layer and cure, which will make the area off-limits for all other construction in the meantime. The results will be great, but you must recognize the potential cost to your timetable.
- 2. Traction – Additive grit to the top layer of an epoxy floor will help prevent slips and accidents, but too much grit can trap dirt and cause havoc with mops and PPE footwear.
- 3. Cleaning – Keep in mind that heavy cleaning will wear out any floor’s protective outer layer over time—epoxy or vinyl. Be sure to understand the manufacturing specifications of the flooring and know when it might be time to re-seal surfaces.
- 4. Traffic – Over time, heavy equipment or carts can wear out even epoxy flooring, so consider anticipated traffic in your design as well as your maintenance budget.
- 5. Durability – You can expect both vinyl and plastic flooring to last about a decade, depending on usage and manufacturer recommendations.
About the Authors:
Chris Hohn has been with AES since 2016, starting his career as an estimator, and transitioning to a project development engineer role in 2019. Chris studied civil & architectural engineering at Drexel University and was always fascinated by unique construction projects and materials. In early 2020, Chris opened the AES west coast office, located in Irvine, California.
Matthew Korkuch is a project manager for AES. He has worked in the construction department since 2012 in a variety of roles. In March of 2020 Matt relocated to AES’ Irvine, CA location in order to better serve west coast clients.